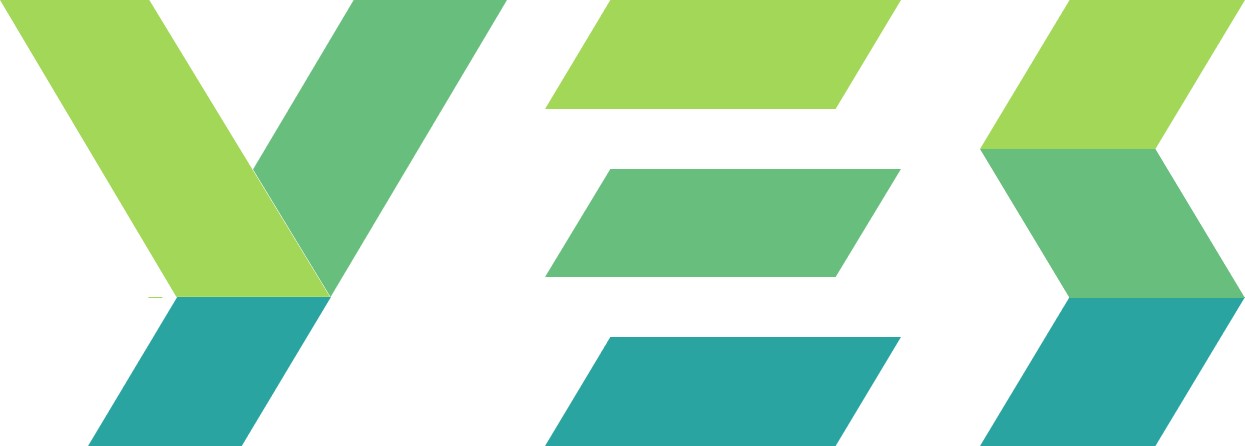
YES (Yield Engineering Systems, Inc.) is a leading provider of process engineering equipment and lab-to-fab solutions for transforming surfaces, materials and interfaces. Product lines at YES include vacuum cure ovens, chemical vapor deposition (CVD) systems, and plasma etching tools used for precise surface modification and thin-film coating of semiconductor wafers, semiconductor and MEMS devices, biosensors and medical substrates.
Additionally, YES offers complete lab-to-fab solutions, Manufacturing as a Service (MaaS), and process/product design services via the renowned YES Applications Labs and Product Development Centers located in North America, APAC, and EMEA. YES is headquartered in Fremont, California.
YES’s technologists are experts in modifying surfaces to encourage bonding between unlike materials. Whether through plasma bombardment, chemical reaction or a combination of the two, YES systems can help solve your adhesion problem.
YES plasma systems gently but effectively remove oxidation and contaminants from bond pads to enable strong adhesion without affecting sensitive electronics.
The ions generated by YES’s environmentally safe oxygen plasma systems bond quickly and completely with metal oxides, leaving behind clean metal surfaces with no substrate damage
In device fabrication, photoresist is used to transfer a pattern onto a substrate. Once the pattern is created in the resist, a descum operation removes trace amounts of resist and other residues. After the pattern is transferred, the remaining photoresist must be removed from the substrate before it can move to the next processing step. YES’s plasma cleaning systems are effective for stripping thick layers of photoresist, as well as descumming, etching, and removing organics.
Whether the substrate is a silicon semiconductor wafer, a glass microscope slide or a plastic microfluidics device, YES cleaning systems provide thorough yet gentle plasma cleaning with no surface damage.
YES plasma systems provide gentle, predictable, tunable surface cleaning without using hazardous solvents, for contamination-free sample preparation. Glass slides, which can vary in quality from batch to batch, can be prepared with plasma for consistent surface coating. In addition, medical device materials including metals (e.g. Ti, Co-Cr) and polymers (e.g. UHMWPE, PEEK) can be properly cleaned, prepared and textured (at micro and/or macro scale) to promote strong adhesion of a broad range of coatings.
Choose from three series of YES Clean Systems for gentle surface cleaning, decontamination, and surface activation. YES Clean Systems can also descum and strip off photoresist using downstream plasma. Unique benefits of YES Clean Systems include:
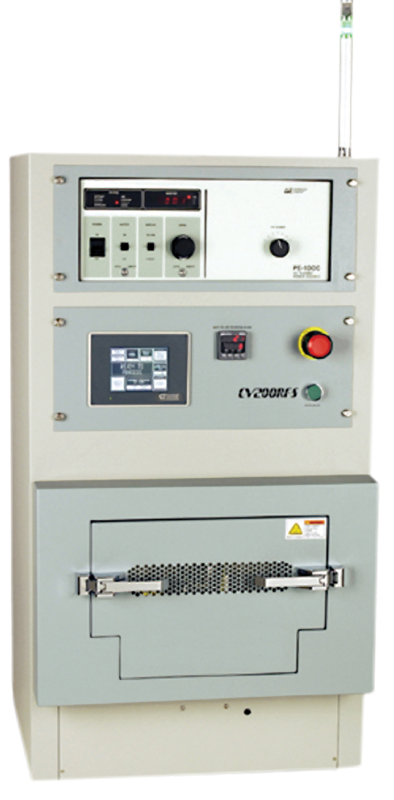
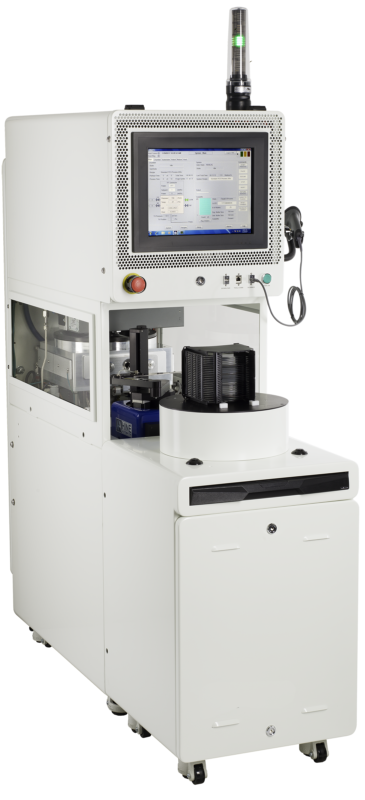
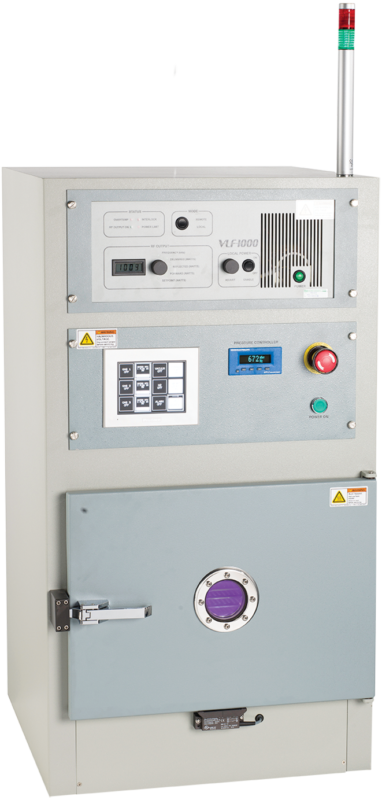
- Reduction in equipment footprint by half over competition
- Lower cost of ownership by almost 50%
- Proven high reliability from system designs with as few as three moving parts
Modify surfaces at the nanoscale with YES Coat Systems, which apply monolayer coatings to induce hydrophobic (water-repelling) or hydrophilic (water-attracting) properties. With YES Coat Systems, coat a variety of substrates with unique benefits including:
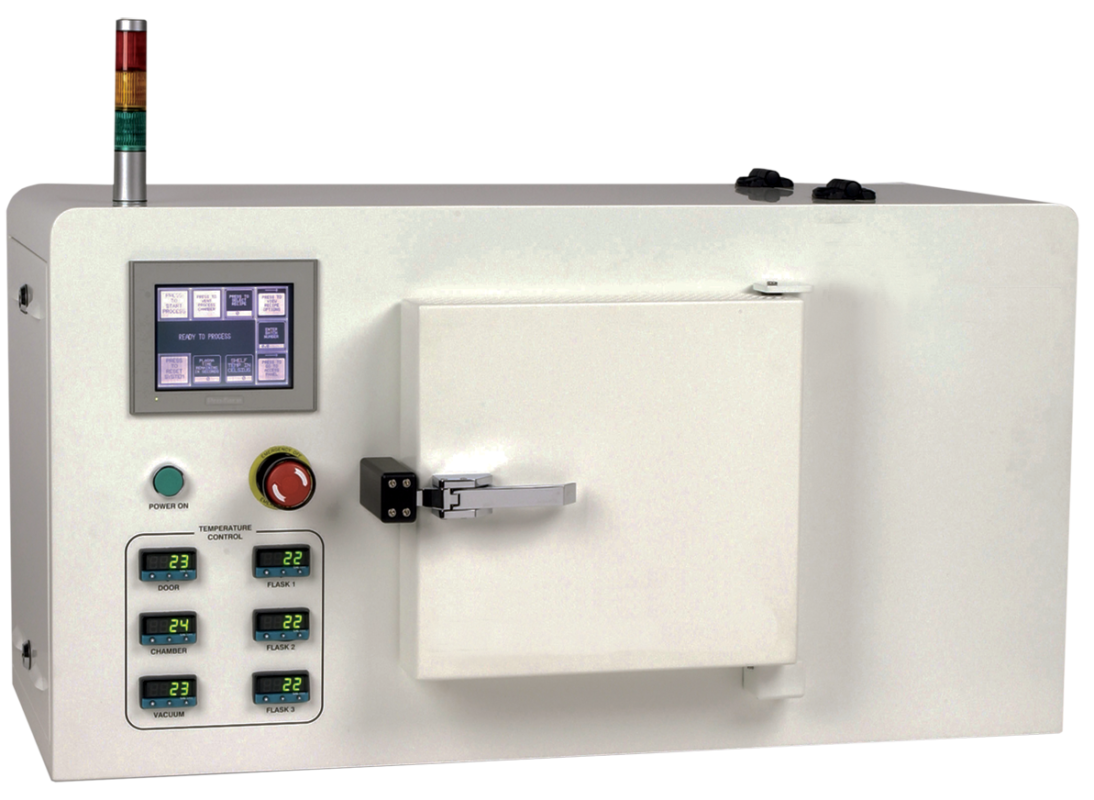
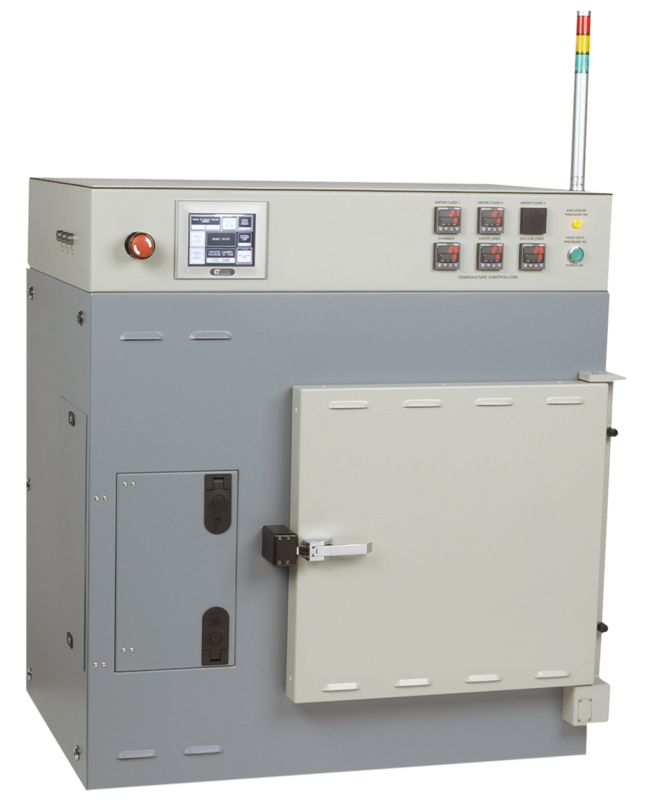
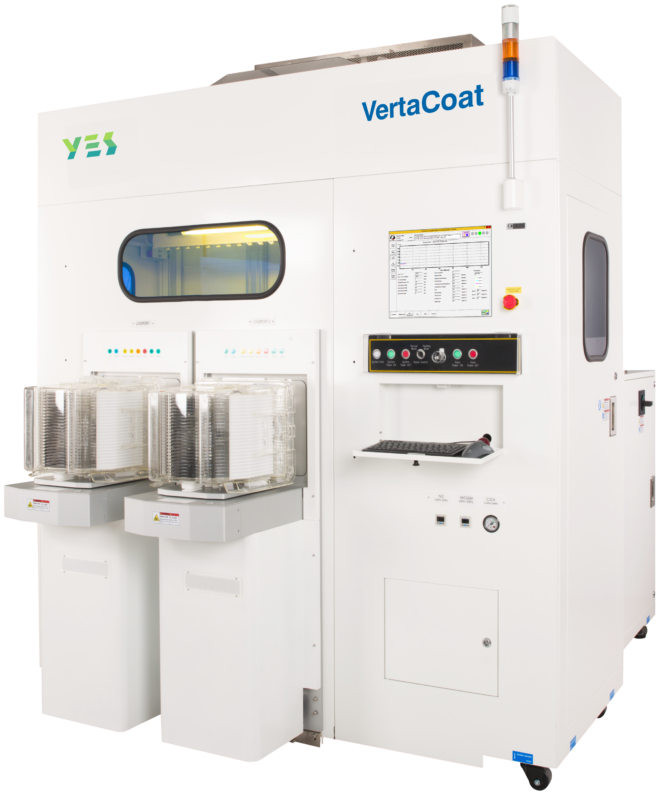
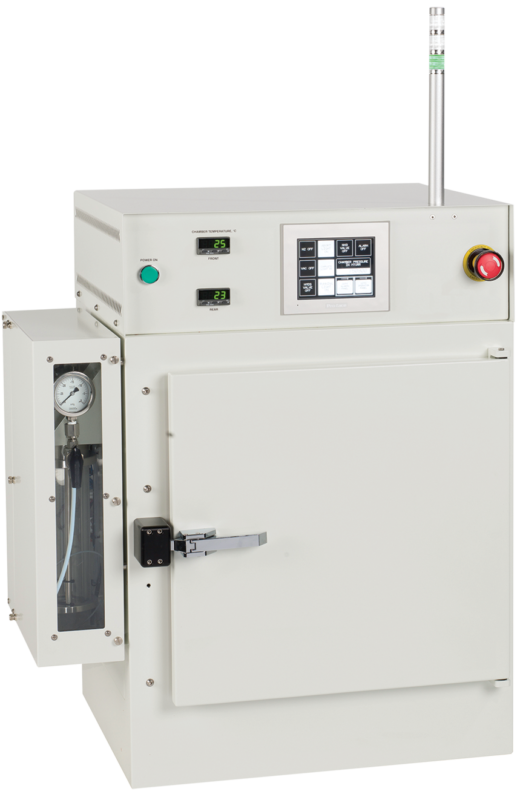
- Choose among 100+ chemical precursors
- Achieve up to 3X improvement in temperature uniformity over our competition
- Leverage YES expertise and proven history in deploying thousands of systems across various emerging industries
Applications
- Surface modification (adhesion/hydrophobic/hydrophilic)
- Adhesion improvement
- Anti-stiction layer
- Surface priming for microarrays
- DNA sequencing and microfluidics
- Self-assembled monolayer deposition and removal
- Seed layer for metallization
Transform materials using thermal and chemical processes via YES Cure Systems for emerging technology and emerging research needs. For instance, semiconductor manufacturers have used YES Cure Systems to cure polyimide precursors for advanced packaging. With YES Cure Systems:
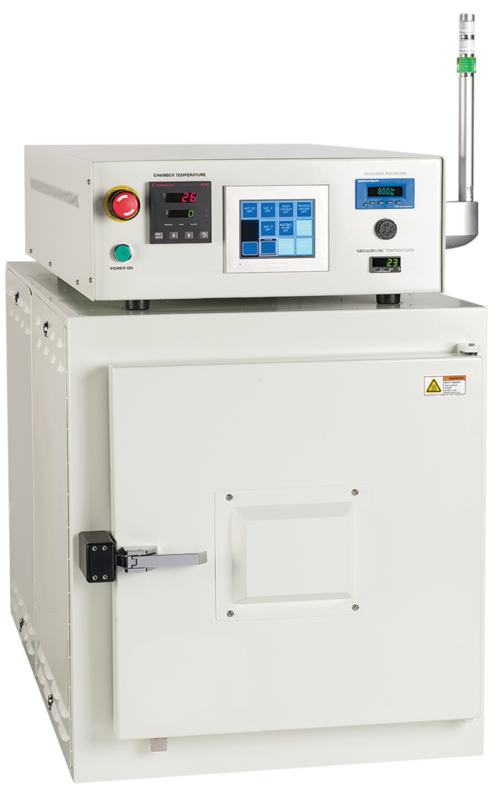
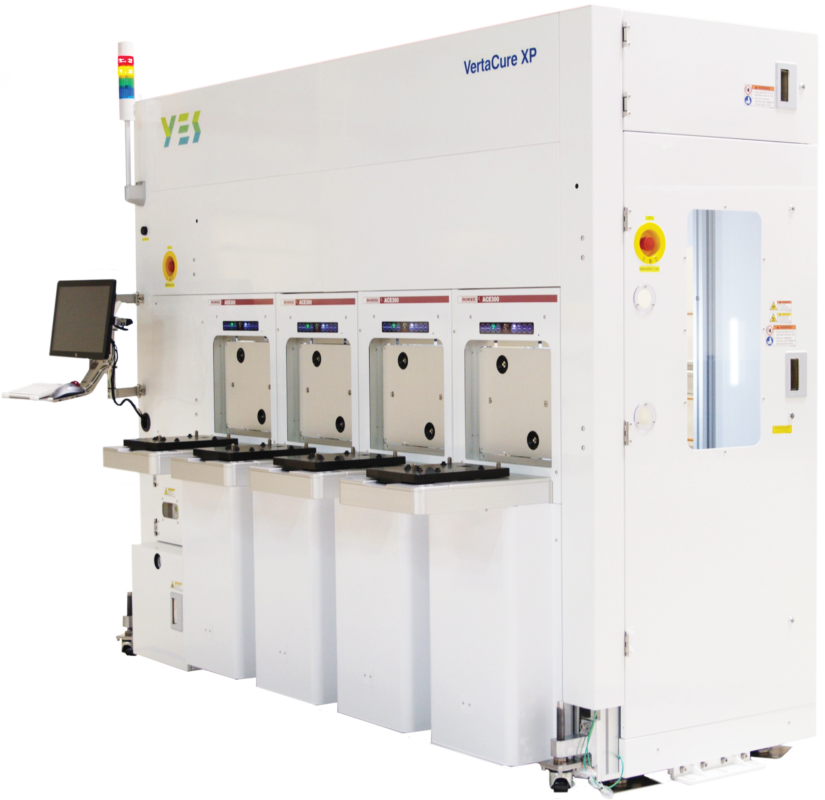
- Achieve up to 50% improvement in cure time
- Cut total cost of ownership (TCO) in half
- Improve the performance of products with less outgassing, greater film stability, and higher reliability
Applications
- Polyimide, BCB or PBO cure
- Wafer-to-wafer bonding anneal
- Vacuum anneal up to 400°C
- Pre-metal or pre-PVD bake and degas